Medical Devices Industry for Rapid Prototyping and Production
Medical devices are known for their complex structure and high requirements for precision and reliability. Tuofa puts higher demands on the workpiece material, processing accuracy and surface finish of medical device parts, which also means that the precision processing capability needs to move to a new level.
Why Medical Device Companies Choose Tuofa?
Agile Response
Create small batch customization production capacity for medical devices, Tuofa is in action! By operating with rapid prototyping in 1 day and small batch production in 7 days, we respond quickly to the individual needs of doctors and patients.
Multiple Materials
Choose from hundreds of materials including engineering plastics with excellent stability, polymers with high machinability, and high-strength metal materials. In reducing manufacturing costs, physicians and patients can enjoy healthcare services at a lower cost.
Technology Leadership
Use the world's most advanced 3D printers and 5-axis CNC machines to create versatile, appearance-oriented, high-precision medical parts trusted by more than 28% of Fortune 500 medical device companies and medical device engineers and medical device designers.
Try Tuofa Now!
Aerospace & aviation equipment consists of millions of precision components with a wide variety of parts and complex designs, and based on the high stability, speed, and safety requirements of the aerospace industry, Toppan has extremely high-quality standards for the design, manufacturing, machining, and assembly of components in all segments.
Tuofa Engineer Support Team - Real human quotes are more accurate than software quotes
|
What Materials Work Best for Custom Medical Instruments?
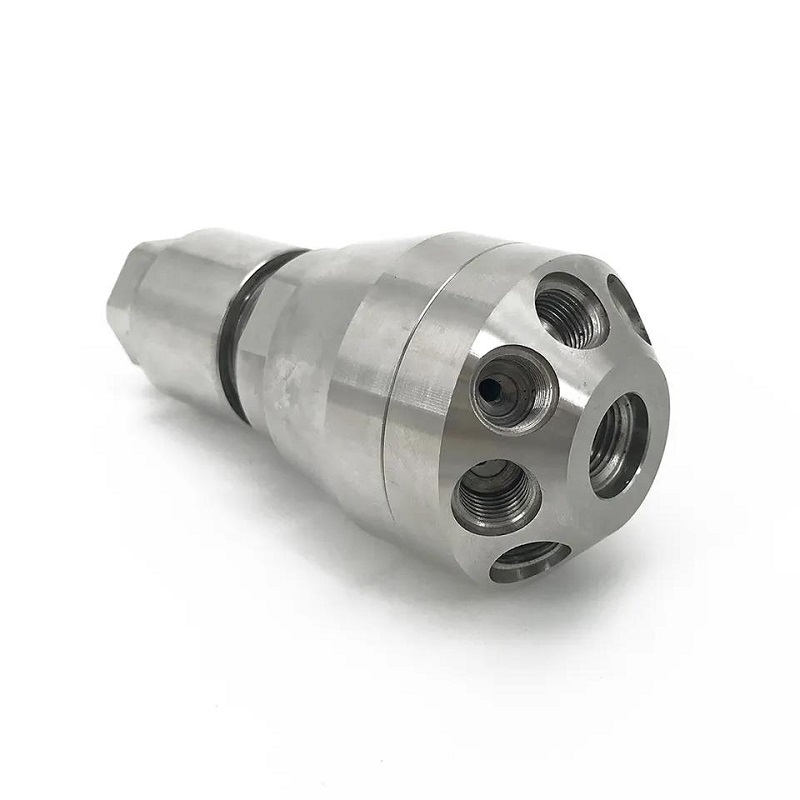
Titanium and titanium alloys are mainly used in orthopedic surgery, especially in limb and cranial reconstruction, for the production of various fracture internal fixation devices, artificial joints, skull and dura, artificial heart valves, teeth, dental beds, brackets and crowns.
Cobalt alloys are more suitable for the manufacture of long-term implants with severe in vivo loading conditions, mainly used for the manufacture of artificial hip joints, knee joints, joint fasteners, bone plates, bone nails and bone pins.
Stainless steel is used for fracture avoidance medical devices: knives, scissors, hemostats, needles, artificial joints, internal fracture fixators, orthodontics, artificial heart valves, etc.
Medical precious metals are the general term for gold (An), silver (Ag), platinum (Pt) and their alloys. Because of their excellent electrical conductivity, they are often used to make implantable electrodes or electronic detection devices.
Polyethylene is among the top medical-grade plastics because of its cost-effectiveness, impact resistance, corrosion resistance and robust structural integrity during frequent sterilization cycles, making it suitable for the manufacture of prostheses.
Polypropylene is stress, crack, impact and fatigue resistant and is used in the manufacture of plastic components for medical devices such as disposable syringes, oxygenator membranes, prescription bottles, connectors and knuckle prostheses.
PVC materials are durable, strong and rigid. It is suitable for the manufacture of hemodialysis devices, catheters, cardiac catheters and prosthetic materials.
Polycarbonate has good heat resistance and biocompatibility and is suitable for the manufacture of medical components such as IV connectors for renal dialysis, cardiac surgery.
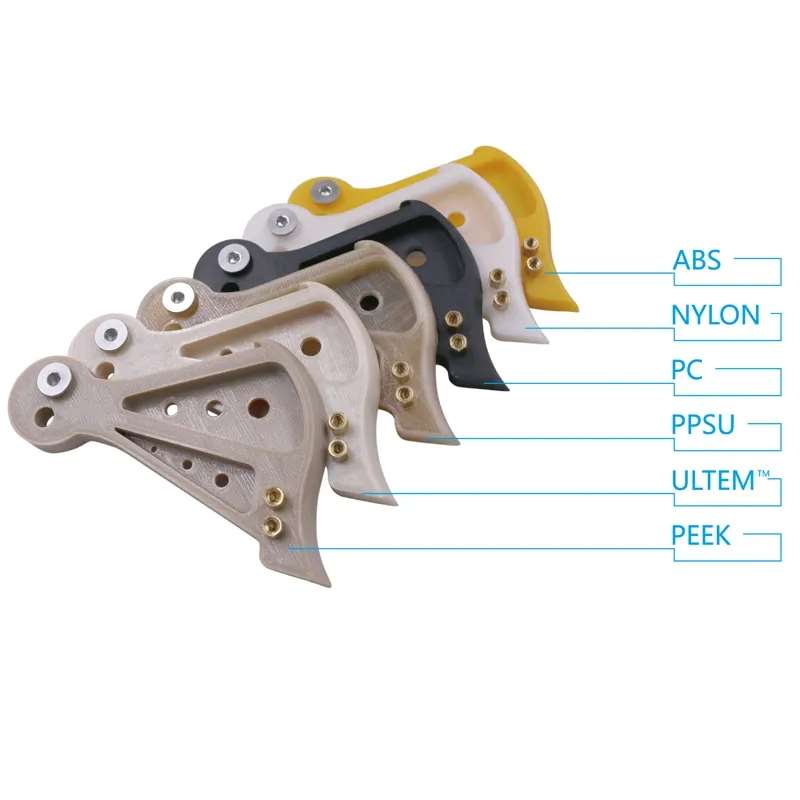
Medical Parts Applications
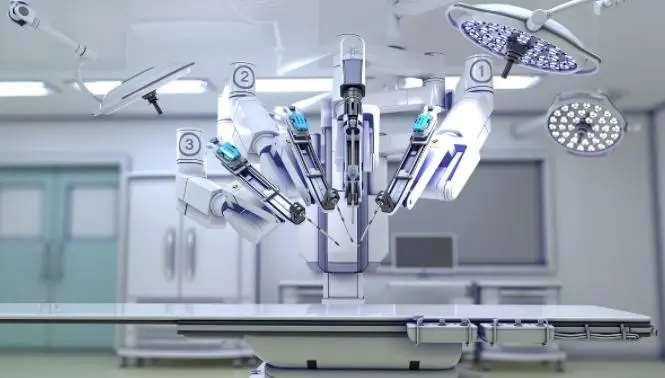
Tuofa can supply you with high-quality medical plastic and metal materials. Regardless of the stages of processing, design, and development, the solutions and experience of our medical engineers can bring you efficient, comfortable and safe products and help you achieve higher product benefits.
Bone Plates
Implant Roots
Cardiovascular Stents
Screws
Knife, Scissors
Hemostat, Needle
Manufacturing Capacity of Medical Industry
Most of the medical parts have the characteristics of small batch, multi-species, irregular shape, hard material, high surface finish, etc. These parts need strict precision manufacturing and quality control, such as orthopedic implants (mostly titanium alloy or stainless steel, with joint plates, artificial joints, bone nails, etc.), dental implants, pacemaker parts, etc.
The medical device industry is growing, and medical device companies continue to look for better manufacturers to enhance their competitive advantage.
Learn more about Tuofa's manufacturing potential for the medical industry.
Custom Medical Component Quote
Gallery of Medical Components
How does Tuofa Innovate Medical Technologies?
Tuofa implements product experimentation and development according to your design drawings, design concepts, specific functional or index requirements, and the whole process relies on the professional skills and valuable experience of our medical engineers.
People Also Ask
Tuofa's conception of 3D printing medical devices
Since 2006, Toppan has been developing and designing medical parts using the latest 3D printing technology. With the advantage of manufacturing complex structures and low volume customization, we are trying to optimize the design and manufacturing of some surgical instruments. Many surgical instruments integrate multiple parts that are assembled together by screws or using welding. The future development direction of metal medical materials
1, physicians and patients want to use the best metal medical materials, long-term use of safety and reliability is the basic requirements for medical metal materials. Therefore, the future development of metal medical materials is still to continuously improve the use of safety, reliability and biocompatibility. What you should know about auto parts?
1. Complexity of auto parts: Every car is made up of nearly 30,000 parts, and only when every part works correctly can a car drive properly, safely and economically. |